Top 10 Best Practices for Optimizing Fulfillment Logistics Operations.
Optimizing fulfillment logistics operations is crucial for businesses to ensure efficient and cost-effective delivery of products to customers. By implementing best practices, companies can streamline their logistics processes and improve overall customer satisfaction. Here are the top 10 best practices for optimizing fulfillment logistics operations:
1. Utilize Advanced Technology
Implementing advanced technology such as warehouse management systems (WMS), transportation management systems (TMS), and automated order processing can significantly improve the efficiency of fulfillment logistics operations. These technologies help in real-time tracking, inventory management, and order processing.
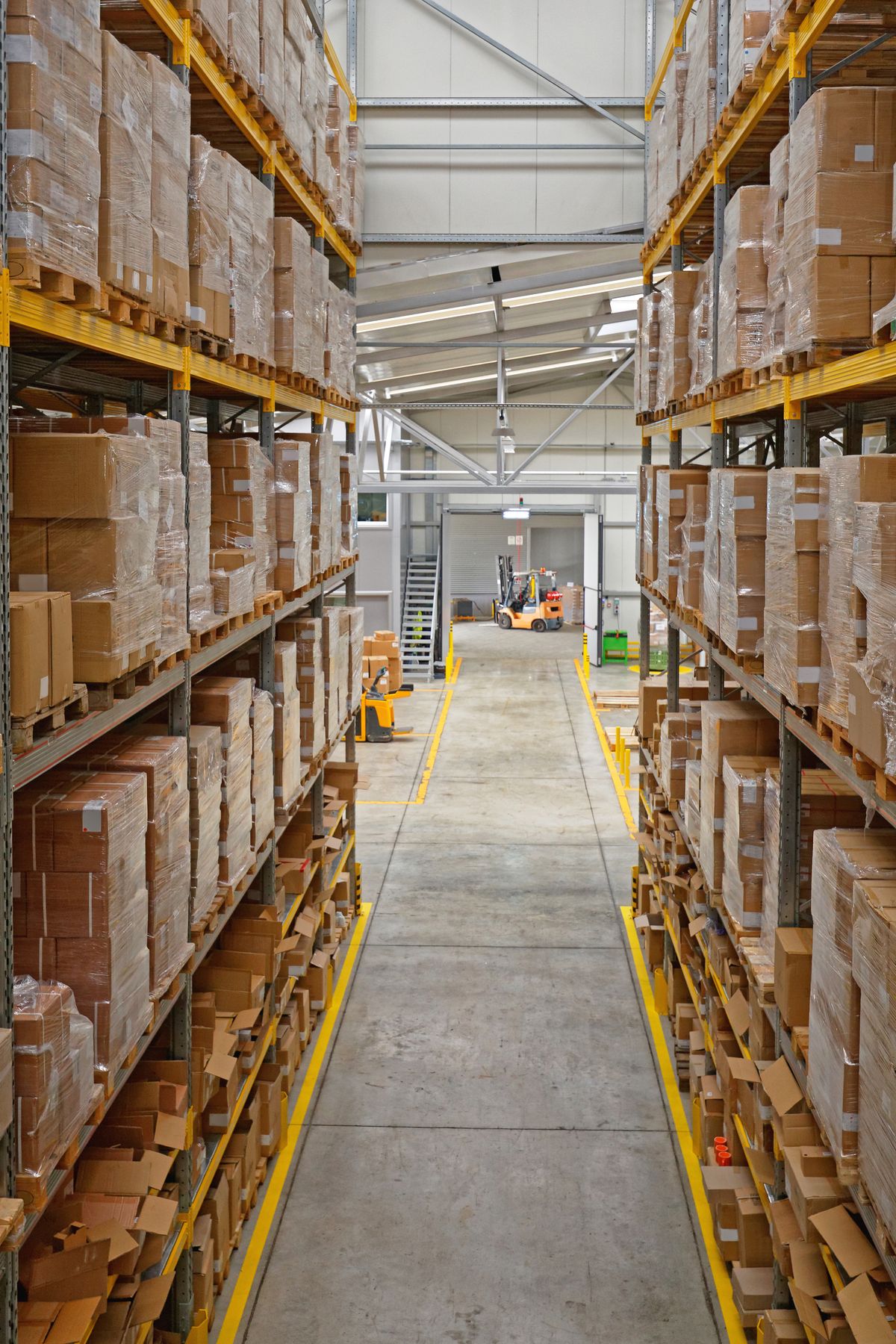
2. Optimize Warehouse Layout
Efficient warehouse layout design plays a critical role in optimizing fulfillment logistics. By organizing products strategically and minimizing travel time for pickers, businesses can reduce fulfillment time and improve overall productivity.
3. Implement Lean Inventory Management
Adopting lean inventory management practices can help in reducing carrying costs and minimizing stockouts. By analyzing demand patterns and maintaining optimal inventory levels, businesses can enhance fulfillment efficiency and reduce storage costs.
4. Enhance Order Picking Processes
Optimizing order picking processes through batch picking, zone picking, or wave picking can improve order accuracy and reduce fulfillment time. By utilizing efficient picking strategies, businesses can fulfill orders more quickly and accurately.
5. Streamline Transportation Management
Efficient transportation management is crucial for optimizing fulfillment logistics. By consolidating shipments, optimizing routes, and utilizing reliable carriers, businesses can minimize transportation costs and improve delivery timelines.
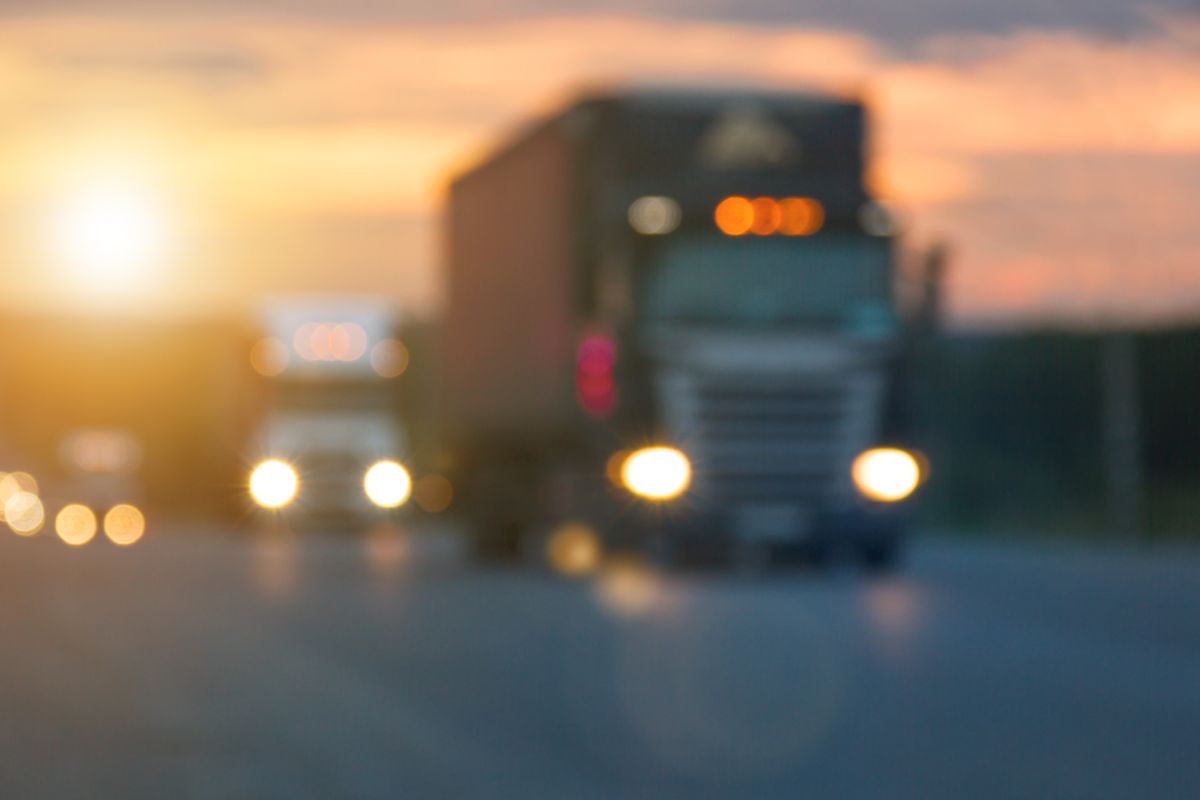
6. Implement Quality Control Measures
Implementing quality control measures at various stages of the fulfillment process ensures that products are accurately picked, packed, and shipped. By minimizing errors and returns, businesses can enhance customer satisfaction and reduce operational costs.
7. Leverage Data Analytics
Utilizing data analytics to track key performance indicators (KPIs) such as order cycle time, fill rates, and on-time delivery can provide valuable insights for optimizing fulfillment logistics operations. By analyzing data, businesses can identify areas for improvement and make informed decisions.
8. Focus on Continuous Improvement
Embracing a culture of continuous improvement is essential for optimizing fulfillment logistics operations. Encouraging employee feedback, implementing process enhancements, and regularly evaluating performance metrics can drive ongoing efficiency gains.
9. Prioritize Customer Communication
Effective communication with customers regarding order status, tracking information, and delivery updates is crucial for a positive fulfillment experience. By providing transparent and timely communication, businesses can enhance customer satisfaction and loyalty.
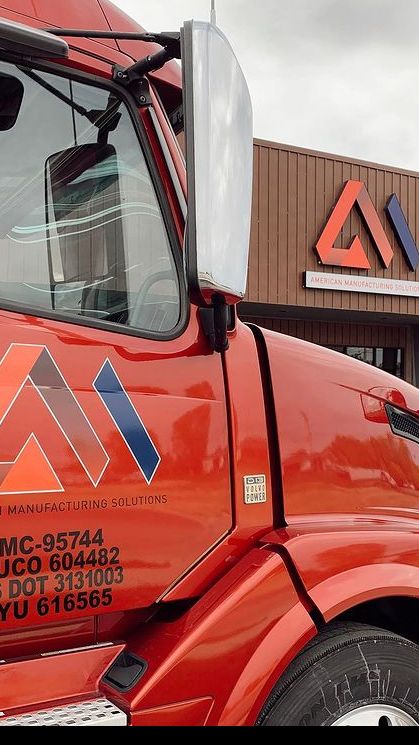
10. Partner with Reliable Suppliers and Carriers
Collaborating with reliable suppliers and carriers is essential for ensuring consistent and timely product availability and delivery. By establishing strong partnerships, businesses can mitigate supply chain risks and optimize fulfillment operations.