How to Optimize Your Fulfillment Process for Peak Performance
Understanding Your Fulfillment Process
In today's fast-paced market, optimizing your fulfillment process is essential for maintaining competitive advantage. This involves analyzing every step from order receipt to delivery and ensuring that each component is functioning efficiently. Begin by mapping out your entire process to identify potential bottlenecks or areas for improvement.
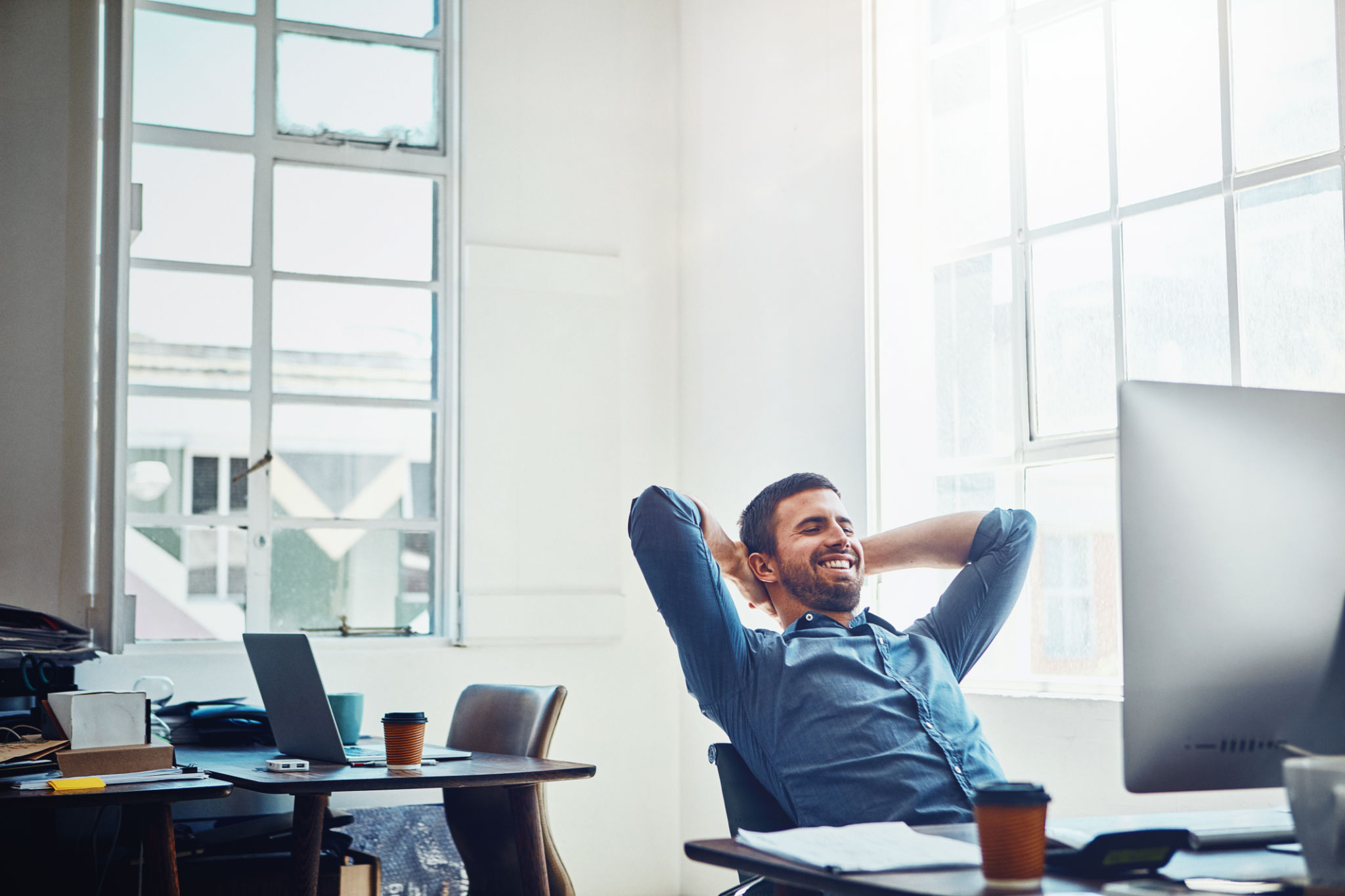
Implementing Technology Solutions
Leveraging technology can significantly streamline your fulfillment operations. Implementing an advanced warehouse management system (WMS) can help automate tasks, reduce errors, and provide real-time data visibility. Additionally, consider using order management software to integrate your sales channels and improve the accuracy of your inventory tracking.
Enhancing Inventory Management
Effective inventory management is crucial for optimal fulfillment performance. Utilize inventory forecasting tools to predict demand and prevent stockouts or overstock situations. Regularly audit your inventory to ensure accuracy and address discrepancies promptly. Adopting a just-in-time inventory approach can also help minimize storage costs while maintaining adequate stock levels.
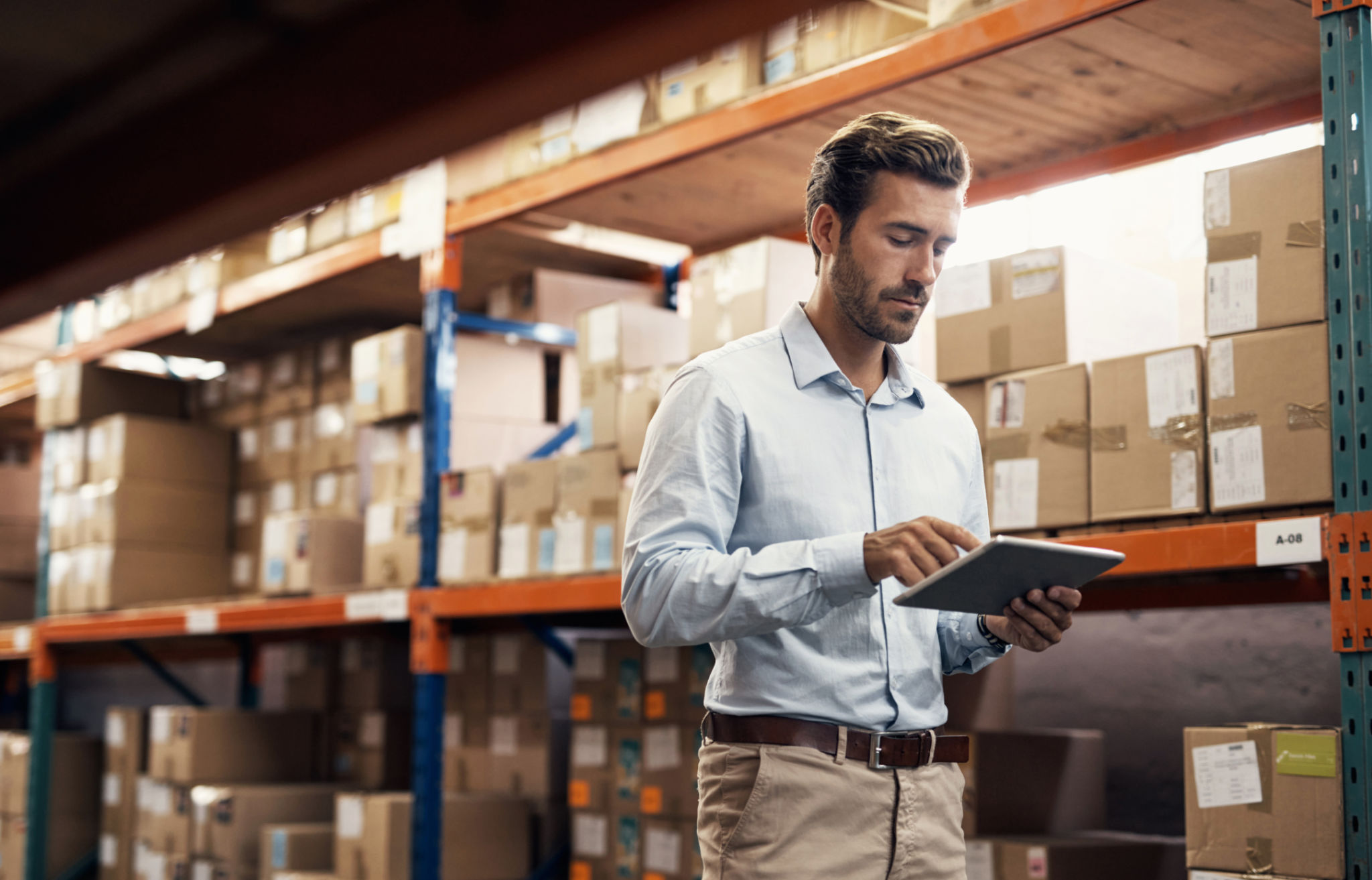
Optimizing Warehouse Layout
An efficient warehouse layout is a critical factor in reducing fulfillment time. Design your space to minimize travel distance by strategically placing high-demand items near packing and shipping areas. Implementing a well-organized shelving system and clear signage can further enhance workflow efficiency.
Improving Order Picking Strategies
The order picking process is often the most time-consuming aspect of fulfillment. Consider adopting different picking strategies such as batch picking, zone picking, or wave picking to suit your specific operational needs. Utilize pick-to-light or voice-directed picking technologies to improve accuracy and speed in the order picking process.

Streamlining Packaging and Shipping
Optimizing your packaging process is essential for reducing costs and improving customer satisfaction. Use size-appropriate packaging to minimize material waste and shipping expenses. Implement automated packing systems and explore partnerships with reliable carriers for faster, cost-effective shipping solutions.
Monitoring and Analyzing Performance
Regularly monitoring and analyzing your fulfillment performance is key to ongoing optimization. Establish key performance indicators (KPIs) such as order accuracy, delivery time, and return rates to measure success. Use this data to identify trends, uncover inefficiencies, and implement targeted improvements.

Fostering Continuous Improvement
Continuous improvement should be at the heart of your fulfillment strategy. Encourage feedback from employees involved in the process and foster a culture of innovation. Regular training sessions can keep your team updated on best practices and new technologies, ensuring that your fulfillment process remains agile and effective.
In conclusion, optimizing your fulfillment process requires a holistic approach that encompasses technology, inventory management, warehouse layout, order picking strategies, packaging, shipping, performance monitoring, and continuous improvement. By focusing on these key areas, you can enhance efficiency, reduce costs, and ultimately deliver a superior customer experience.